I started the day by fixing the central and front dividers to the tank pattern having first given it 5 coats of release agent, Oasis foam was glued to the right hand side and the dividers bonded to the foam. It went quite well so I thought I had better quit that job before my luck changed.
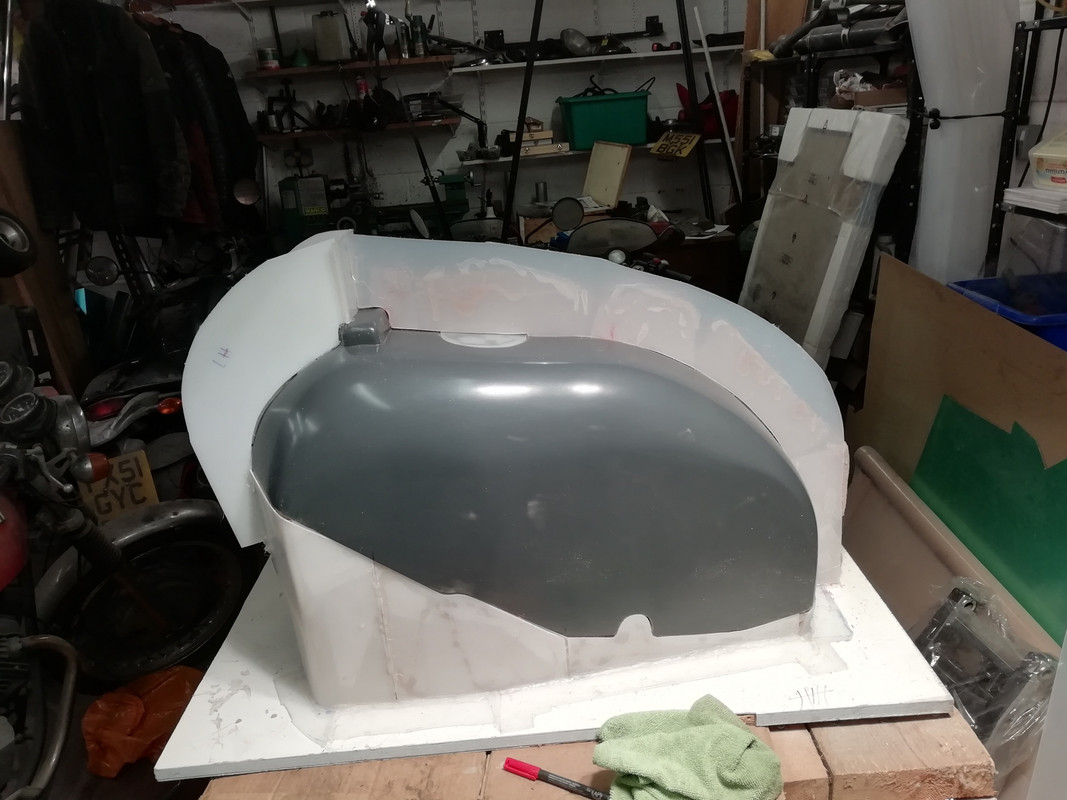
I then spent some time modifying the seat pattern, removing the nib between the base and the seat hump. I had to use the Dremel on the wood screws holding it on and I needed some filler to repair the inevitable damage This nib was initially necessary to join the two halves of the pattern together but now gets in the way of providing a useful size opening for the tool/glove box to be located in the seat hump. I think I have worked out how to do it now. When the seat is formed it will have an open bottom and I will then continue the base from underneath to the rear end of the hump by bonding in a shaped sheet of CF (formed on a glass plate), this “diaphragm” will form the floor of the glove box.
The near vertical leading edge of the seat hump will have an ambla covered foam pad glued to a CF backing plate. This backing plate will have 2 x tabs that will fit into slots at the junction between the seat base and the hump (forming a crude hinge) and will be secured by a Dzuz fastener at the apex of the hump. The CF backing to this seat pad will effectively be the lid to the glove box.
To provide some form of positive closure to the glove box I cut some 3mm polypropylene to enable a) the hole for the opening to be recessed by 3mm (this will be sealed with a rubber moulding) and b) an indentation to permit the wire captive part of the Dzuz fastener to be flush with the surface of the seat hump. I also started on a mould for the backing plate for the seat hump pad with a 3mm projection that fits into the recess to be moulded into the seat hump itself.
I also started the laborious process of putting 5 coats of release agent on each of the completed moulds.
I am running out of things to make from CF, 2 remaining possibilities are for the rear number plate hanger and the rear LED stop, tail light/indicator holder currently made in aluminium but quite heavy and a little untidy to look at.