The two things achieved today were
a) a mould for a CF rear light/camera mounting which was then laminated; and
b) a mould for the rear number plate which will incorporate a fairing to mask the seat latch mechanism also laminated.
With regard to a) I glued some 1mm polypropylene to a sheet of plywood and then glued on top the profile of the light holder cut from 3mm polypropylene with some 10mm estate agent board also cut to the same profile to act as packing between them. I then cut some 1mm polypropylene to form a smooth upstand that the LED strip lights can be attached to.
I cut this on a large radius curve so that the upstand would sit at an angle to the base such that when it was attached to the bike the lights are vertical not pointing upwards at 30 degrees.
In glue-ing the profiled bits I displaced the top 3mm polypropylene about 3mm forward in an attempt to make the replicate the angle.
When I hot glue gunned the 1mm upstand to the mould, as the hot glue cooled the polypropylene moved a bit and despite my best efforts the actual angle achieved was something like 80 degrees when I had hoped for 60 degrees.
With regard to b) I used a Cornish ice cream plastic tub to form a mould. The base of the tub was slightly profiled so I cut some 1mm polypropylene to line the bottom. This will fit between the two rear frame rails and extend downwards to provide the mounting point for the number plate. Above the frame rails it will be cut at an angle that matches the slope of the seat base and it will extend forward to cover the seat latch mechanism. Below the frame rails the open box will be cut at an angle so that at the bottom there is a stiffening return of maybe 6mm whilst at the top the box will be full height (if that makes sense).
To mount it I will cut from the CF sheet already made a plate that will attach to the truncated frame tubes and this plate will be slotted into the triangular cut box and then be bonded in. Confident it should work and will be light in weight. It has the advantage that I can manufacture in stages and get each relative angle right rather than trying to do it all at once (issues are angle of the bottom of the seat, depth of the truncated box necessary to cover the latch mechanism and provide sufficient slope for the number plate to clear the rear tyre on full suspension compression and the angle of the downward facing truncated rear frame tubes and the threaded bushes therein.
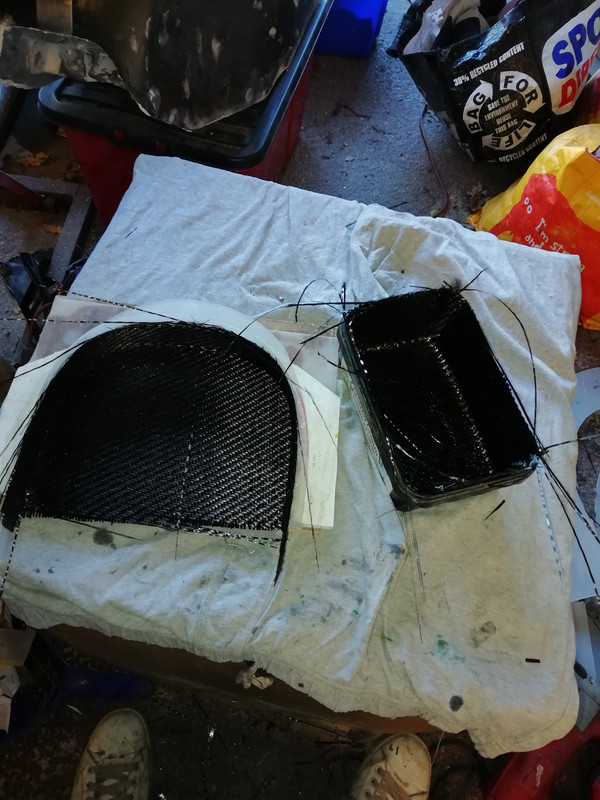