that's great advice Utopia, thank you!
now one of the more satisfying jobs… exhaust fabrication! the original headers were 28mm but its very hard to get any sorts of bends in that diameter so I went up to 32mm, which aesthetically I think looks better. 32mm bends are available in quite a few angles, its just deciding which ones you need, and that’s just an eyeball thing.
Its not that difficult to make a system, its more time consuming. Cuts are made using a 1mm cutting disk in the angle grinder, and if you wrap masking tape around the cut line you can get it very accurate. then it’s a matter of assembling it together, initially with Jubilee clips. I cut slots in these so I can tack it in situ. A tip about tacking is to double the amps on the welder to what you would use to weld… and then put the tiniest of tacks in place. A tiny tack also has the advantage that it does not pull a gap on the opposite side that you will get if you make big ones. Three tiny tacks are actually very strong, but if you make a mistake, can easily be broken by touching them with the cutting disk.
Note the 2 way spirit level… this is a VERY useful (and cheap!) way of making sure build lines are correct. If you have the bike vertically (using a long spirit level on the wheel) and horizontal you can place the 2 way level on the bike and tape it there… that becomes your datum. To get it right on this bike I had to drop the stanchions through the yokes as I will be replacing the 19″ front wheel with a 17″ on soon.
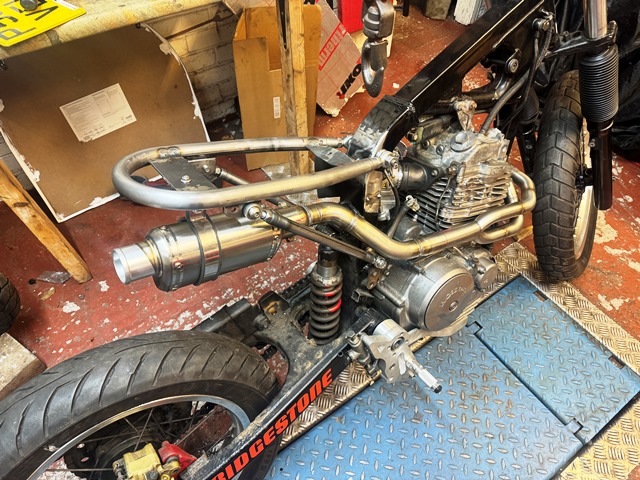