A frustrating day in the garage today, entirely avoidable and all my fault. I decided it was time to put the frame on the engine so everything trial fitted to the frame had to come off first.
I found the titanium studs I made up previously. I had been recommended to weld a titanium nut on one end to facilitate screwing the studs into the captive threaded portions on the lateral tubes on the RH side of the frame. I never got round to this so I resorted to grinding a slot with a 1mm cutting disc on one end of the stud. I made a bit of a Horlicks of the first one as the shower of dazzling white sparks caused me to lose my line and to cut the slot off centre.
Next, I needed to make some undersize nuts as a standard 10mm nut has 17mm flats and there is not enough room to get a 17mm socket inside the lateral tube and over the nut. I should have paid more attention to you guys when this was raised earlier.
I decided to bore out 4 x 8mm flanged nuts rather than a standard 8mm nuts as they fit nicely inside the tubes and the flange has anti-vibration serrations stamped onto the mating surface.
One disadvantage of this plan is that as flanged nuts are stamped out rather than just parted off a piece of hexagon bar, the flats are slightly conical to facilitate release from the press during manufacture. Gripping them in a vice or the lathe means that there is only a point contact rather than across the whole flat which means they wobble about when drilling and when trying to tap them out.
In order to get 4 reasonably good "undersize" nuts with concentric holes and perpendicular threads I had to make 6, which took a couple of hours as my 8.5mm drill
was a cheap one and refused to stay sharp (one day I will learn and stop buying cheap drills).
When I came to trial fit them I realised that the powder coating had compromised the first thread which was duly cleaned out with a large hand-turned countersink bit. I then realised that the thread in the frame was M10 x 1.0 and I had threaded the studs M10 x 1.25.
Measure twice and cut once!!!
The studs are now scrap.
I turned my attention next to the exhaust studs, I want to fit dome-headed stainless nuts to prevent corrosion/erosion of the studs/nuts and to achieve this the studs have to be shortened. I wish I had remembered this before I put the heads back on as hacksawing the studs at awkward angles and with the crankcase in the way was a bit laborious.
Finally, I tried to put the engine on the frame, after about 20 minutes of struggling it was obvious that the powder coating on the inside of the lateral tubes would have to come off as there is no discernable "spring" in the frame. This meant about an hour with a small flat file. It's funny how when you want the powder coating to come off it is really hard and resilient but if you drop a 10mm spanner on it from about 3 inches it leaves a mark.
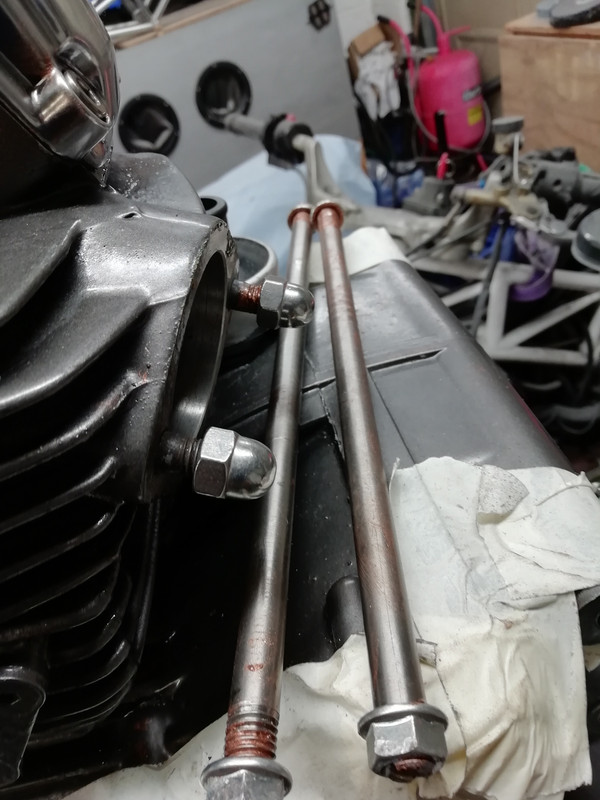